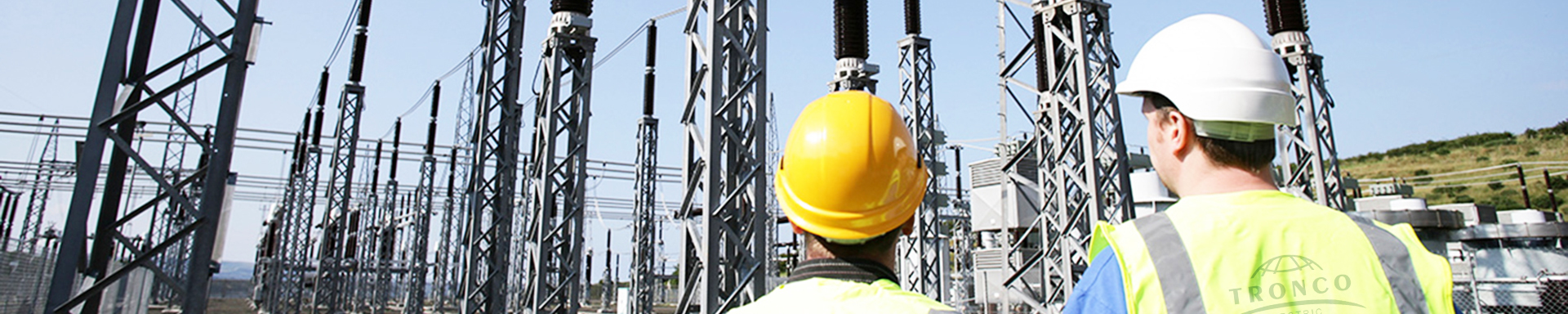
Herstellung hochwertiger Isolatoren aus gehärtetem Glas
2022-11-07 20:28Qualität ist ein Maß für Exzellenz und wird in der Elektrizitätsindustrie anhand einer Vielzahl nationaler oder internationaler Standards wie ANSI, IEEE, IEC, ASTM usw. gemessen. Obwohl die Erfüllung dieser Standards natürlich von entscheidender Bedeutung ist, haben die meisten diese Standards erkannt Heutzutage stellen nur minimale Leistungsanforderungen in einer Anwendung dar. Aus diesem Grund versuchen sowohl Hersteller als auch Anwender, die Produktqualität durch verbesserte Spezifikationen weiter zu differenzieren. Qualität bezieht sich auch auf die Herstellung. Standards und kontinuierliche Prozessverbesserung konzentrieren sich dabei auf Kontrollen und Wiederholbarkeit mit dem Ziel von Null Fehlern. Letztlich muss Qualität neben der Einhaltung von Grundnormen und Kundenspezifikationen auch Produktfähigkeit und Langlebigkeit repräsentieren.
Die Herstellung von Isolatoren aus gehärtetem Glas kann als aus zwei Hauptschritten bestehend angesehen werden: Herstellung der Glashülle und dann Montage von Metallbeschlägen auf dieser Hülle. Die Produktion erfordert spezielle Ausrüstung und nur wenige Hersteller weltweit verfügen über die Ressourcen und Erfahrung, um beide Schritte in einer einzigen Produktionsstätte durchzuführen. Dabei ist es sinnvoll, die Qualität nicht nur bei der Herstellung der ESG-Schale, sondern auch später bei der Endmontage des Isolators zu betrachten.
Die gehärtete Glasschale bildet den eigentlichen Isolator. Auch die Fittingmontage und deren Zementierung sind wichtig, diese Hülle muss jedoch über die gesamte Lebensdauer intakt bleiben, um die Produktfunktionalität zu gewährleisten. Darüber hinaus sollte nach dem Zusammenbau das Auftreten eines Schalenbruchs, der nicht durch ein äußeres Ereignis verursacht wurde, selten sein. Die allgemeine Industrieerwartung ist beispielsweise, dass weniger als 1 von 10.000 installierten Einheiten pro Jahr spontan zerbrechen sollte. Daher ist das Auftreten von Selbstzertrümmerung ein Aspekt der Herstellung, um dessen Minimierung die Fabrik bemüht sein muss.
Abgesehen von der kritischen Schale gehören zu den Hardwarekomponenten eines Isolators aus gehärtetem Glas:
1. Kappen
Die obere Kappe ist eine verzinkte Muffe aus duktilem Gusseisen, die mit einem Sicherungsstift aus Edelstahl montiert wurde.
2. Stifte
Der untere Bolzenbeschlag ist eine Kugelverbindung aus geschmiedetem Stahl, die verzinkt und mit bituminösem Teer beschichtet wurde. Für eine erweiterte Leistung, insbesondere in rauen Betriebsumgebungen, kann auch ein Opferkragen aus Zink hinzugefügt werden.
Bei niedrigeren Spannungen werden manchmal Gabelkopf-/Zungenbeschläge verwendet.
3. Rohglas & Ofen
Die Herstellung der Glasschale beginnt mit wichtigen Rohstoffen und Zutaten, darunter Siliziumdioxid, Aluminiumoxid, Natriumcarbonat, Natriumsulfat, Kalkstein, Pottasche und Dolomit. Bruchglas (manchmal auch als Saatglas bezeichnet) ist Glas, das aus der früheren Herstellung recycelt und diesen Rohstoffen zugesetzt wird, um die Konsistenz von Charge zu Charge zu gewährleisten. Das Mischen dieser Materialien ist für jeden Hersteller spezifisch und sieht geringfügige Abweichungen bei Elementen vor, die aus lokalen Quellen abgebaut oder im Ofen verwendet werden. Diese natürlichen Schwankungen in Mineralien erklären den geringfügigen Unterschied, der im Farbton der isolierenden Glasschale beobachtet wird.
Öfen sind typischerweise großräumig mit einer Kapazität von über 100 Tonnen. Für Konsistenz ist es wichtig, die Temperatur aufrechtzuerhalten und auch die Chemie des Outputs sowie die Mischung der zugeführten Rohstoffe regelmäßig zu überwachen. Der Ofen ist die erste mögliche Quelle für Einschlüsse – Fehler im Glas, die schließlich dazu führen können spontanes Zerbrechen. Zum Beispiel können feuerfeste Steine mit der Zeit beginnen, das Material in die Glasmischung abzulösen. Öfen müssen daher alle paar Jahre zur Wartung stillgelegt und neu zugestellt werden.
Schalenbildung
Dies geschieht auf einer automatisierten Presse, wobei eine genaue Menge geschmolzener Glastropfen in den Formhohlraum eingeführt und gepresst wird (siehe Abb. 1). Die Abmessungen der einzelnen Schalen, dh Höhe und Durchmesser, sind durch Normen definiert, aber Geometrie und Schalenprofil können sich von Anbieter zu Anbieter unterscheiden.
Härteprozess
Nach dem Formen durchläuft die Schale einen speziellen Prozess, bei dem sie von der Presse zu einer Härtungslinie transportiert wird und einen Homogenisierungsofen durchläuft, um das Glas auf einer konstant hohen Temperatur zu halten. Das Vorspannen des Glases wird durch schnelles Abkühlen des heißen Glases unter Verwendung von Druckluft an Schlüsselstellen entlang der Schale erreicht, um eine gleichmäßige Abkühlung zu erreichen. Dies führt dazu, dass das Glas eine heiße Kerntemperatur, aber eine relativ kühle Oberfläche hat. Die Glasstruktur sieht nach dem Härten das Zentrum unter Spannung, während die Oberfläche unter Druck steht, und dies erhöht den mechanischen und elektrischen Widerstand sowie die Haltbarkeit der Isolierteile aus Glas. Das Erreichen einer einheitlich hohen Qualität in diesem kritischen Schritt erfordert einen hochgradig automatisierten und sorgfältig kontrollierten Materialhandhabungsprozess.
Thermischer Zyklus
Nach dem Vorspannen werden die Schalen durch einen vorgeschriebenen thermischen Zyklus geführt, wo sie einem thermischen Schock ausgesetzt werden, mit dem Ziel, potenziell fehlerhafte Schalen zu extrahieren. Die Schalen werden auf etwa 300°C erhitzt und dann in kaltes Wasser getaucht, wodurch die Temperatur des Glases effektiv auf 120°C gesenkt wird. Unzureichend gehärtete Glasschalen werden durch den plötzlichen Temperaturschock zusammenbrechen. Jede Schale wird mindestens einmal thermisch geprüft und bei Bedarf kann der gesamte Vorgang wiederholt werden. Der Thermoschockzyklus ist im Wesentlichen eine Schlüsselqualitätsprüfung, da jede Schale, die platzt, eine ist"No Go"während Muscheln, die überleben, ein 'Go' sind. Glasschalen, die während der thermischen Zyklen zusammenbrechen, werden recycelt, wobei Fragmente gesammelt und in Form von Scherben (Saatglas) dem Produktionsprozess wieder zugeführt werden.
Betrieb des Ofens ist"24/7"und damit schneller als der Montageprozess. Aus diesem Grund werden fertige Schalen bis zur Montage auf Lager gehalten. Kappen- und Stiftmontage Glasschalen werden in die Kappen zementiert, während die Stift- und Zinkhülsen mit Tonerdezement in die Schale zementiert werden. Auch hier wird Automatisierung eingesetzt, um eine genau abgemessene Zementmenge sicherzustellen und eine genaue Längentoleranz zu erreichen. Die zementierte Anordnung wird dann durch zyklisches Durchlaufen eines einstündigen Bades in Wasser bei etwa 70°C gehärtet. Jeder ESG-Isolator wird nach dem Aushärten einer elektrischen und mechanischen Stückprüfung sowie abschließenden Sichtkontrollen unterzogen.
Elektrische Routineprüfung: kontinuierlicher Überschlag für 4 Minuten,
Mechanischer Routinetest: gehalten bei 50 % der SML-Bewertung für>3 Sek.
An jeder konfektionierten Isolatorencharge werden dann Stichprobenprüfungen durchgeführt. Dies umfasst die Überprüfung aller kritischen Abmessungen, die Einhaltung der Fassungs-/Kugellehre, die Überprüfung des Verriegelungssystems, die Verzinkungsprüfung, den M&E-Test und den Impulsdurchschlagtest.
Validierungs- und Testberichte
Fertige Isolatoren werden Design- oder Qualifizierungstests gemäß Industriestandards unterzogen, einschließlich ANSI C29-2B, IEC 60383, CSA-411-1-16 und GOST 6490-93. Kunden können ihren Spezifikationen auch zusätzliche Testkriterien über diese Standards hinaus hinzufügen, um die endgültige Isolatorleistung weiter zu qualifizieren.
Testberichte für jedes Isolatordesign sollten spezifisch für das Werk sein, in dem der Isolator hergestellt wird. Wenn ein Lieferant zwei Fabriken hat, die den gleichen Isolatortyp herstellen, sollte es separate Design-/Qualifizierungsberichte für jeden Isolator speziell für das Werk geben, in dem er hergestellt wurde. Für Produkte, die an einem anderen Ort montiert werden, sollten Testberichte für diese einen Hinweis darauf enthalten, in welcher Fabrik die Schale hergestellt wurde. Wenn die Schalen aus gehärtetem Glas aus zwei Fabriken stammen, sollte dies separate Testberichte vorschreiben (dh spezifisch für die Fabrik, die die Schale hergestellt hat).
Schlussfolgerungen
Bei der Betrachtung der Qualität eines Isolators aus gehärtetem Glas sollten die Bewertung und Qualifizierung gründlich sein und jeden Aspekt der Produktion umfassen. Es sollte besonders darauf geachtet werden, wo die Hülle aus gehärtetem Glas hergestellt wird und wie dieser Prozess aufrechterhalten wird, um zu verhindern, dass defekte Hüllen jemals bei der Montage fertiger Isolatoren verwendet werden. Der Grund dafür ist, dass die Montage der Kappe und des Stifts zwar wichtig ist, die Qualität der Hülle aus gehärtetem Glas jedoch einen größeren Einfluss auf die langfristige Isolatorleistung hat. Testberichte sollten spezifisch für die Fabrik sein, in der der Isolator hergestellt wird, aber auch darauf hinweisen, wo die Hülle hergestellt wurde. Dies würde spezifische Werkskennzeichnungen erfordern. Das Gehäuse aus gehärtetem Glas sollte zumindest Markierungen aufweisen, die in seinen Körper eingegossen sind, einschließlich M&E-Bewertung, Chargencode-Referenz, und Fabrikidentifikation (ID). Diese Markierungen sollten lesbar und dauerhaft sein. Die ID der Fabrik, in der der Isolator montiert wird, sollte auf der Kappe des Isolators angebracht sein – ebenfalls lesbar und dauerhaft. Selbst wenn sie in derselben Fabrik hergestellt werden, helfen solche Markierungen sowohl auf der Schale als auch auf der Kappe zu erkennen, wann die Schale hergestellt und wann sie zusammengebaut wurde. Das Anbringen von Fabrik-ID-Markierungen an der Hülle ist einfach, mit geringen Auswirkungen auf die Produktkosten, bringt aber ein höheres Maß an Qualitätssicherung für die Isolatoren. Die verschiedenen Industriestandards (z. B. ANSI, IEC, CSA) fordern nicht ausdrücklich eine Fabrik-ID auf einer Shell, sollten es aber vielleicht tun. Selbst wenn sie in derselben Fabrik hergestellt werden, helfen solche Markierungen sowohl auf der Schale als auch auf der Kappe zu erkennen, wann die Schale hergestellt und wann sie zusammengebaut wurde. Das Anbringen von Fabrik-ID-Markierungen an der Hülle ist einfach, mit geringen Auswirkungen auf die Produktkosten, bringt aber ein höheres Maß an Qualitätssicherung für die Isolatoren. Die verschiedenen Industriestandards (z. B. ANSI, IEC, CSA) fordern nicht ausdrücklich eine Fabrik-ID auf einer Shell, sollten es aber vielleicht tun. Selbst wenn sie in derselben Fabrik hergestellt werden, helfen solche Markierungen sowohl auf der Schale als auch auf der Kappe zu erkennen, wann die Schale hergestellt und wann sie zusammengebaut wurde. Das Anbringen von Fabrik-ID-Markierungen an der Hülle ist einfach, mit geringen Auswirkungen auf die Produktkosten, bringt aber ein höheres Maß an Qualitätssicherung für die Isolatoren. Die verschiedenen Industriestandards (z. B. ANSI, IEC, CSA) fordern nicht ausdrücklich eine Fabrik-ID auf einer Shell, sollten es aber vielleicht tun.